So you’ve decided to manufacture your product in China. The country offers a wealth of opportunities for businesses looking to produce high-quality goods at competitive prices. However, if you’re not cautious, the geography and sheer scale of manufacturing can often lead to a lack of quality assurance in China.
Fortunately, there are tried-and-true best practices for managing quality assurance in China when sourcing or manufacturing in the country. Implementing these guidelines can mitigate risks, optimize your production cycle, and ultimately ensure customer satisfaction.
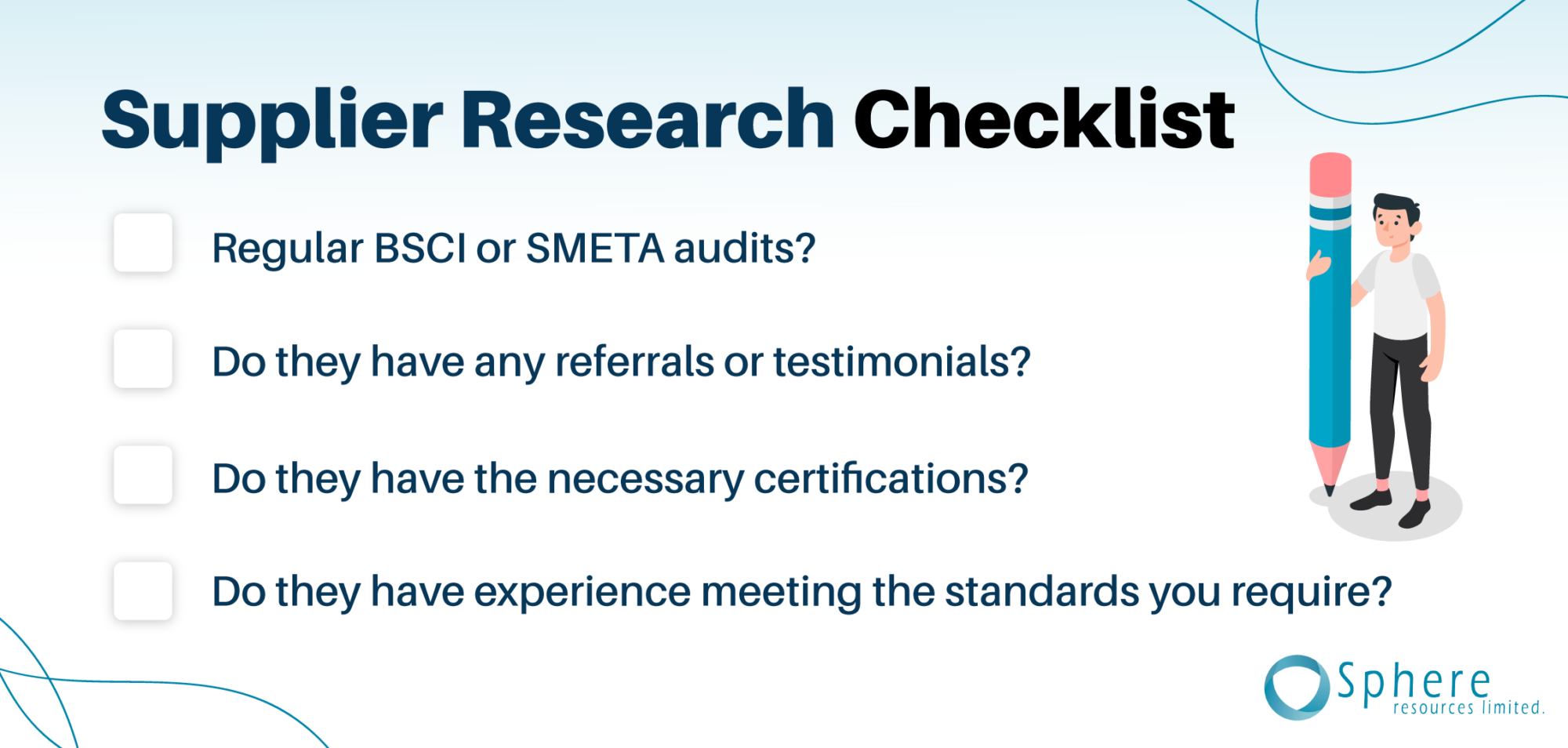
1. Conduct Initial Supplier Research
Before even thinking about your first shipment, you’ll need to conduct rigorous supplier research. Start by looking into their background, past performance, and client testimonials. An essential credential to consider is the ISO 9001 certification, an international standard that assures a basic level of quality management and operational processes within an organization.
Additionally, look into whether the supplier has social compliance audits like BSCI (Business Social Compliance Initiative) or SMETA (Sedex Members Ethical Trade Audit). These audits can provide further assurance of the supplier’s ethical and social practices. You can learn more about the differences and importance of these through this BSCI vs SMETA guide.
Not only should you ask for these certifications, but you should also independently verify their authenticity. In some cases, suppliers have been known to falsify certificates to attract business. A quick verification process can save you a lot of trouble in the long run. Moreover, consider doing an initial pilot run to gauge the supplier’s capability and reliability before committing to a full-scale operation.
2. Use Quality Assurance in China Checklists
Crafting a thorough checklist is an essential step, and resources like this guide on creating checklists can offer valuable insights. It should be a living document that both parties understand and agree upon. This list can serve as the blueprint for product expectations, detailing measurements, tolerances, material types, and industry-specific requirements.
Involve multiple departments in the creation of this checklist. For instance, your engineering team can help specify technical criteria, while your marketing team can give input on aesthetic factors like color or packaging. Once the checklist is complete, share it with your supplier and make sure they fully comprehend each element.
3. Insist on Material Certifications
The quality of your final product is only as good as the raw materials used. Ensure that your supplier can provide certifications for all the raw materials they’re using. Certifications should conform to both international and industry-specific standards, such as RoHS (Restriction of Hazardous Substances) for electronics.
Going a step further, consider engaging a third-party laboratory to test the raw materials independently. It’s an additional cost but could save you from significant issues down the line, such as recalls or reputational damage. For example, leveraging labs accredited by ISO can provide that extra layer of quality assurance.
4. Develop a Quality Control Timeline
Your quality assurance in China is an ongoing process that should be integrated throughout the production cycle. Work with your supplier to create a quality control timeline that outlines the various stages for inspections. This could include checks after the receipt of raw materials, post-assembly, and right before shipping.
Make this timeline transparent and hold your supplier accountable for it. If they miss a deadline or fail an inspection, have a contingency plan in place. This could be as simple as an additional round of quality checks or as severe as terminating the contract.
5. Conduct On-Site Inspections
While photos and virtual meetings offer some level of oversight, there’s no replacement for on-site inspections. These inspections can either be conducted by your in-house team or through a third-party inspection service. Regular, unannounced visits can provide the most authentic view of daily operations.
On-site inspections allow you to review the work environment, speak directly with factory employees, and witness the manufacturing processes firsthand. These visits are not just about finding flaws; they’re also opportunities to build relationships and understand your supplier’s capabilities and limitations.
6. Quality Assurance in China: Leverage Technology
Modern quality management software provides valuable tools for overseeing your manufacturing process remotely. Such software can facilitate real-time communication, data collection, and trend analysis, helping you identify issues before they become significant problems.
Invest in technology that integrates with your supplier’s systems for a seamless quality control process. Look for features like real-time analytics, dashboard overviews, and mobile capabilities that allow you to monitor quality metrics on the go.
7. Quality Assurance in China: Train Your Suppliers
The most effective quality control processes are collaborative. Don’t assume that your supplier understands your quality expectations. Take the initiative to train them on your specific standards, processes, and requirements.
Offer to send a team over for an initial training session or use video conferencing to conduct this training remotely. It’s an upfront investment of time and resources, but clearly defining expectations will help minimize misunderstandings and errors in the long run.
8. Monitor Packaging and Shipping
The manufacturing process doesn’t end when your product rolls off the assembly line. Poor packaging and storage can compromise product quality, negating all your previous quality control efforts. Ensure that packaging materials meet your quality specifications and that they are appropriate for the types of shipping and storage your products will undergo.
Request to inspect a few sample shipments before they’re sent out, scrutinizing how products are loaded, secured, and isolated. This will help identify any adjustments that need to be made before large-scale shipping commences.
For comprehensive insights on shipping and logistics services, consider our shipping and logistics solutions.
9. Quality Assurance in China: Regularly Update Quality Standards
The business landscape is always changing, driven by consumer trends, technological advancements, and new regulations. Your quality control procedures should be just as dynamic. Periodically revisit your quality standards to ensure they align with current market demands and regulatory requirements.
Conduct regular reviews involving key stakeholders, like your quality control team, legal advisors, and even customer representatives, to make sure your standards are not just current but also comprehensive.
10. Build Strong Relationships with Suppliers
Successful quality control in China is built on a foundation of good relationships. Cultivate strong lines of communication with your suppliers. Regular check-ins, either virtual or in-person, can go a long way in preemptively identifying potential issues.
Trust, but verify. Being too lax can result in overlooked details, while being too stringent can strain the relationship. Strike a balance by having clear contracts and open channels of communication. Supplier loyalty often results in better quality products and priority service, so never underestimate the value of a good relationship.
Conclusion
Quality assurance in China is a complex, ongoing endeavor that requires diligence, effective communication, and a strong foundational strategy. By implementing these best practices into your operations, you are better positioned to ensure the consistent quality of your products. Given the competitive and ever-changing nature of manufacturing in China, keeping quality at the forefront is not just an option; it’s a necessity.
Want to simplify this complexity? Sphere Resources can handle your quality control processes on the ground for you. Our team of Chinese and Australian staff are experienced QC experts and can create custom quality control solutions based on your needs.
Contact us today to learn more about how we can help.